Made In Space Receives NASA Award to Advance Space-Based Manufacturing
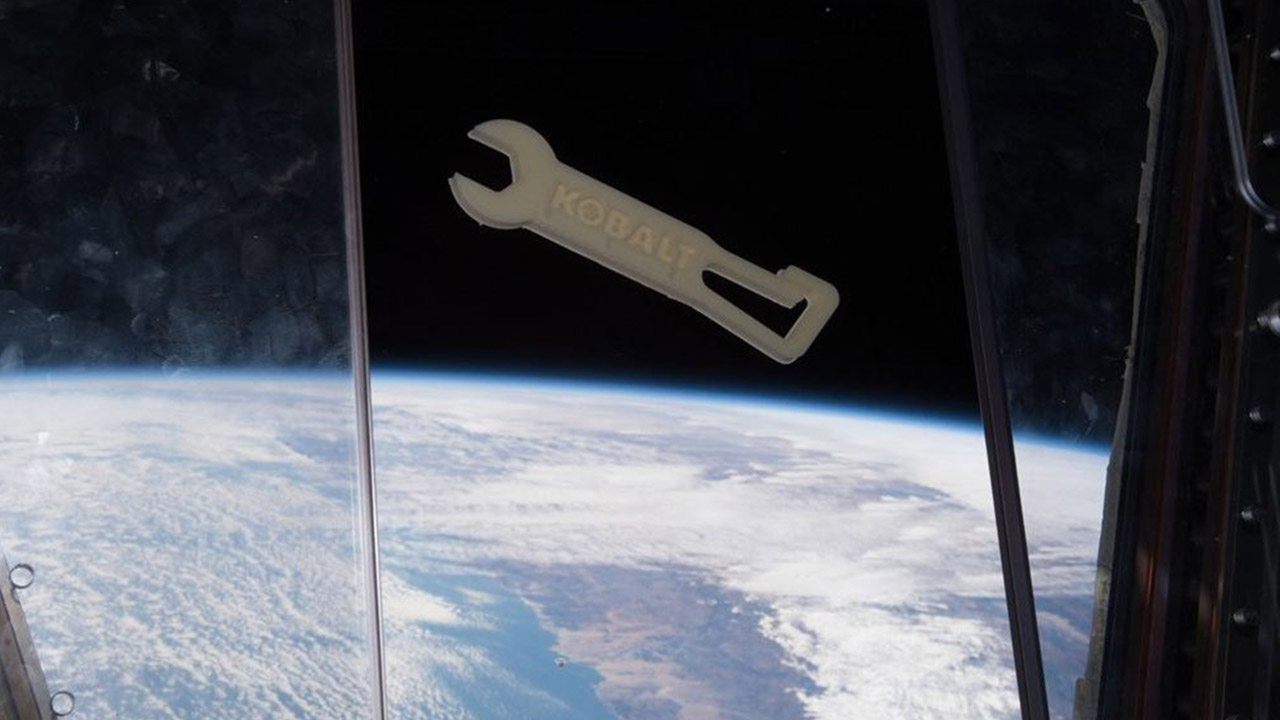
A space-optimized wrench for ISS crew members 3D-printed onboard the space station using the Additive Manufacturing Facility.
Media Credit: Made In Space
April 15, 2020
Last week, Made In Space received an award from NASA supporting two new proposals focused on space-based manufacturing: one to develop a Glass Alloy Manufacturing Machine (GAMMA) for the International Space Station (ISSInternational Space Station) and the other to develop an autonomous, high-throughput manufacturing capability for high-quality, lower-cost semiconductor chips.
With GAMMA, Made In Space will examine how glass alloys form in microgravityThe condition of perceived weightlessness created when an object is in free fall, for example when an object is in orbital motion. Microgravity alters many observable phenomena within the physical and life sciences, allowing scientists to study things in ways not possible on Earth. The International Space Station provides access to a persistent microgravity environment., where gravity-driven forces such as sedimentation and convection are minimized. The team expects in-orbit production will enable significantly higher-quality glass products with applications in optical fibers, lenses, and optical devices for the telecommunications, sensor, and laser technology industries.
Similarly, Made In Space anticipates the reduced sedimentation and convection in microgravity to enable the fabrication of semiconductor chips with fewer defects than chips manufactured on Earth. With the NASANational Aeronautics and Space Administration award, the company will explore the benefits of space-based semiconductor production, with applications in the telecommunications and energy industries.
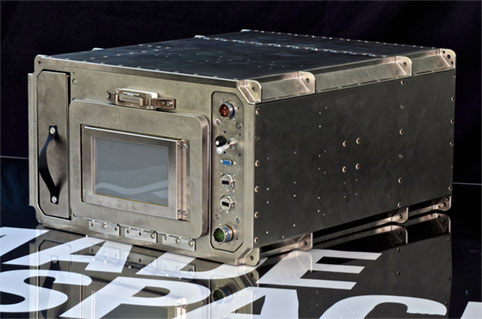
The Additive Manufacturing Facility (AMF) at Made in Space headquarters.
Media Credit: Made in Space
Made In Space has provided 3D printing capabilities on the ISS since the company’s first prototype 3D printer was installed in 2014. Following this prototype, the Additive Manufacturing Facility (AMF) has served as a permanent “machine shop” on the ISS for the past four years, providing in-orbit fabrication services and producing more than 100 tools and other objects for crew members to use while in orbit.
Made In Space also developed a Commercial Polymer Recycling System (CPRS) to demonstrate plastic recycling capabilities in microgravity. The CPRS, which launched on Northrop Grumman’s 12th commercial resupply services mission(Abbreviation: CRS mission) A CRS mission is a cargo resupply mission contracted by NASA to deliver supplies and research to the International Space Station on commercial spacecraft as part of the CRS contract with three commercial companies. As part of CRS missions, experiments currently return to Earth on SpaceX Dragon spacecraft that splash down in the ocean. in November, is designed to work with the AMF and process plastic waste such as plastic bags and expended polymer parts into feedstock for 3D printing.
Additionally, Made In Space is one of three commercial companies working to demonstrate the space-based manufacturing of ZBLAN optical fiber. ZBLAN has the potential to perform up to 100 times more efficiently than traditional silica-based fibers. However, when ZBLAN is produced on Earth, gravity-driven forces lead to imperfections in the fiber. Production in microgravity results in significantly fewer imperfections, leading to valuable high-quality fibers for applications such as repeaterless transoceanic transmission, sensors for aerospace and defense industries, and improved medical devices such as laser scalpels.
For more information on the award to Made In Space, see NASA’s press release.