Making Innovative Ideas Reality
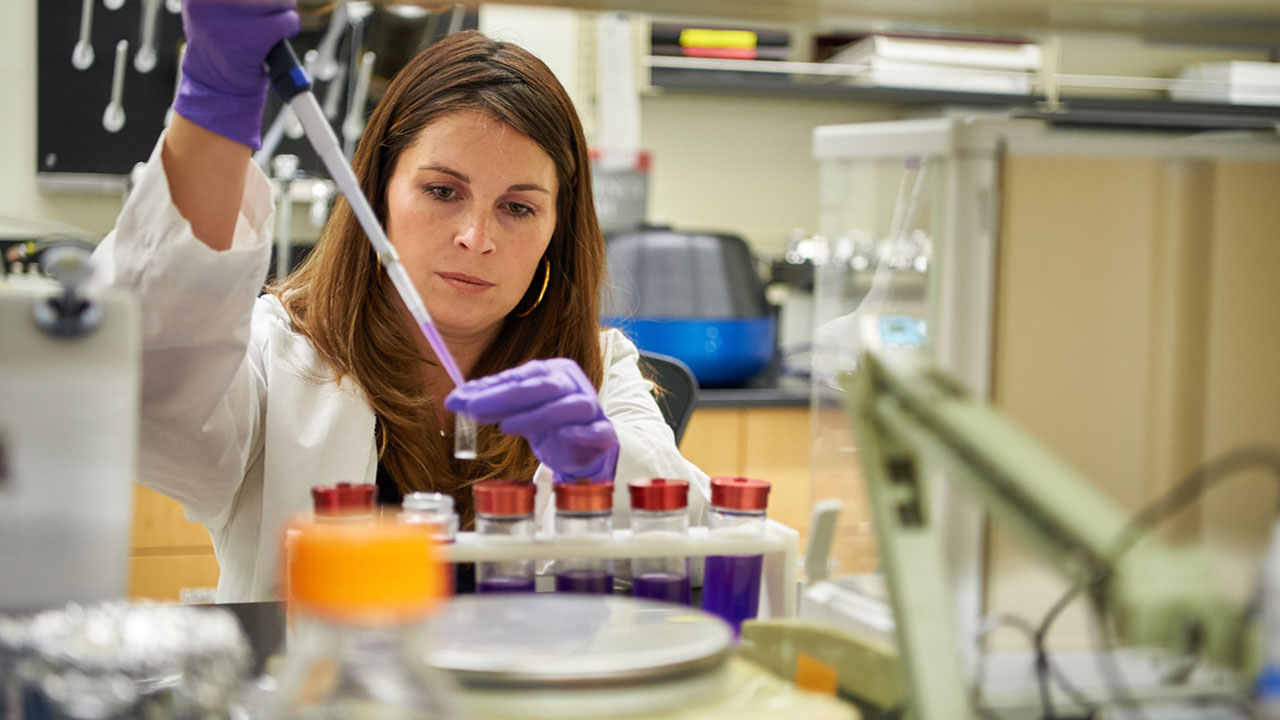
LambdaVision President and CEO Nicole Wagner purifying the protein for use in the retinal implant.
Media Credit: Peter Morenus/UConn Photo
October 23, 2019 • By Nicole L. Wagner, President and CEO of LambdaVision
Nicole L. Wagner is the CEO of LambdaVision, a startup based in Farmington, Connecticut that began as a spinoff company from a University of Connecticut research group. LambdaVision was awarded a MassChallenge “Technology in Space PrizeA prize that provides grant funding for business startups participating in the MassChallenge startup accelerator program to conduct innovative research and technology development utilizing the ISS National Lab. The prize is funded by the Center for the Advancement of Science in Space, which manages the ISS National Lab, and Boeing.” from the ISSInternational Space Station National Laboratory and Boeing in 2016.
At the 2019 ISS Research and Development Conference, Wagner was a panelist in the session “Accelerating Startups in Space,” which discussed how the ISS National Laboratory is serving as a business accelerator in space. At the conference, Wagner also received a 2019 International Space Station Research Award for Innovation in Biology and Medicine.
(Photo courtesy of LambdaVision)
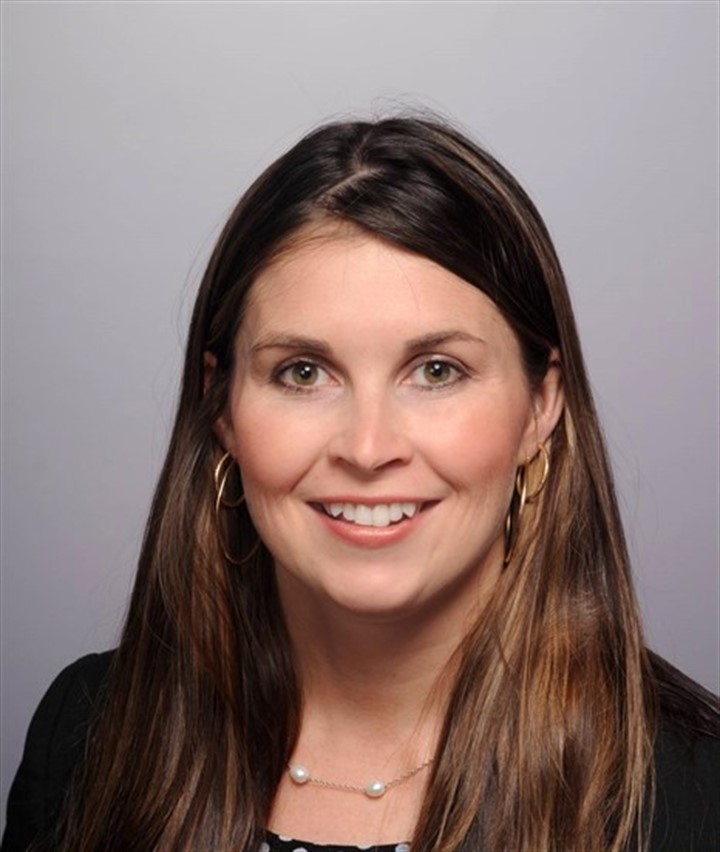
Entrepreneurs have a different way of looking at things. With an “anything is possible” mentality and the belief that there is limitless potential, entrepreneurs can take what might seem like a crazy idea and turn it into a reality. To some people, manufacturing a retinal implant on the International Space Station (ISS) is just that—a crazy idea. But at LambdaVision, we are making it a reality.
LambdaVision has developed a protein-based retinal implant to restore vision to the millions of people blinded by end-stage retinal degenerative diseases, including age-related macular degeneration and retinitis pigmentosa. The retinal implant is produced through a layer-by-layer deposition process, and on Earth, gravity-driven forces such as sedimentation interfere with the uniformity of the layers. Manufacturing the implant in the microgravityThe condition of perceived weightlessness created when an object is in free fall, for example when an object is in orbital motion. Microgravity alters many observable phenomena within the physical and life sciences, allowing scientists to study things in ways not possible on Earth. The International Space Station provides access to a persistent microgravity environment. conditions on the ISS National Laboratory improves the homogeneity of the protein layers, resulting in increased stability and optical quality of the multilayer system. These improvements could lead to the need for fewer layers, which would reduce the amount of materials required, lower costs, and accelerate production time.
The idea for spaceflight research began in 2016 when LambdaVision was accepted into the MassChallenge Accelerator Program in Boston. The ISS National Laboratory and Boeing sponsor a “Technology in Space Prize” for companies seeking to use the ISS and space to improve life on Earth. We put together a proposal to examine the effects of microgravity on the layer-by-layer manufacturing process to create our protein-based retinal implant. To be honest, spaceflight was not really on our radar before becoming part of MassChallenge, but together with the ISS National Laboratory and Boeing, our proposal became a reality.
You may wonder how a non-space company gets to space; however, you don’t have to be a space company to do research on the ISS. We were paired with an Implementation Partner(Abbreviation: IP) Commercial companies that work with the ISS National Lab to provide services related to payload development, including the translation of ground-based science to a space-based platform. to help us with the “space stuff” and with translating our research idea into a flight-ready project. The implementation partner took the stress out of the process and allowed us to focus on things that were in our wheelhouse—the need for the science and how the microgravity environment could be used to benefit people on Earth.
Since our initial flight to the ISS on SpaceX’s 16th commercial resupply services mission(Abbreviation: CRS mission) A CRS mission is a cargo resupply mission contracted by NASA to deliver supplies and research to the International Space Station on commercial spacecraft as part of the CRS contract with three commercial companies. As part of CRS missions, experiments currently return to Earth on SpaceX Dragon spacecraft that splash down in the ocean., we have learned a lot about our experimental design and the effects of microgravity on the layer-by-layer manufacturing process. We are continuing to work on the manufacturing parameterization, and have been working closely with our implementation partner, the ISS National Laboratory, and NASANational Aeronautics and Space Administration, as we explore low Earth orbit(Abbreviation: LEO) The orbit around the Earth that extends up to an altitude of 2,000 km (1,200 miles) from Earth’s surface. The International Space Station’s orbit is in LEO, at an altitude of approximately 250 miles. manufacturing of the implant.
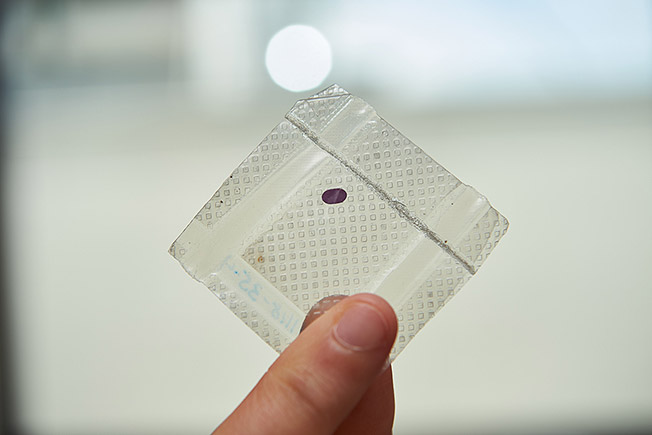
LambdaVision’s tiny protein-based retinal implant. The implant is the small purple dot, which is about the size of a paper hole punch.
Media Credit: Peter Morenus/UConn Photo
In addition to the value of using the ISS to improve our manufacturing process, we also found great value in the partnerships we formed. By leveraging the experience of the ISS National Laboratory, Boeing, and NASA, we were able to expand the expertise of our team and gain connections to investors and key opinion leaders in the field.
For anyone with the “crazy” idea of doing research on the ISS, I would say to start the conversations early and keep the dialogue open. We came in with different ideas, and the ISS National Laboratory and Boeing were willing to talk through what is practical. By starting those conversations, we were able to mold our application and the science around it. If it turns out that your idea is not a good fit for the ISS or microgravity, you’ll find out right away, which can save a lot of time.
I would encourage anyone thinking about conducting an investigation on the ISS to channel your inner entrepreneur and know that space-based research is not out of the realm of possibility. Crazy ideas are sometimes the best ones and are often where innovation begins—don’t be afraid to make your crazy idea a reality!