Purdue Researchers to Study Radiation-Tolerant 3D Printed Metals on the ISS
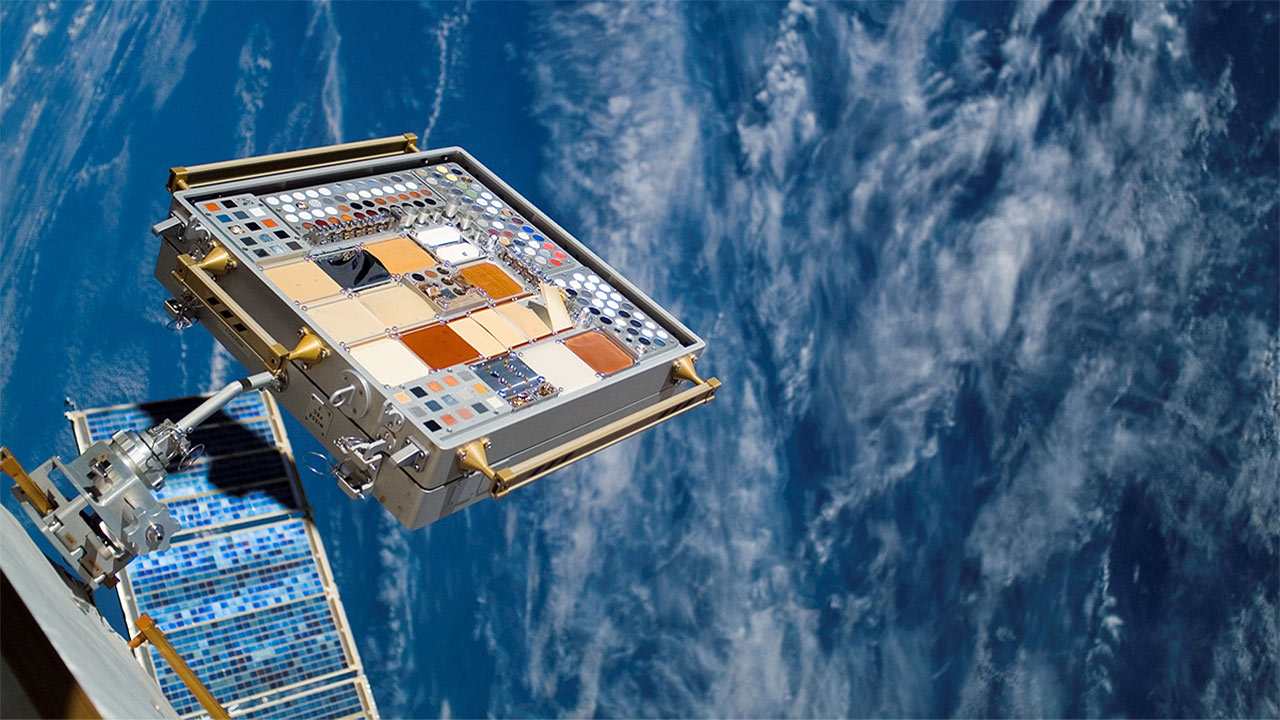
Media Credit: NASA
October 1, 2020
What if the 3D printing of some metals could be controlled to make the metals resistant to radiation damage? Such 3D printed materials could improve metal component lifetimes in high-radiation environments such as deep space or nuclear reactors on Earth. Researchers at Purdue University will leverage the International Space Station (ISSInternational Space Station) to test the ability of specially structured 3D printed metals to withstand radiation damage by exposing them to the extreme environment of space.
This investigation was awarded through an ISS U.S. National Laboratory solicitation for flight experiments that use the MISSE Flight FacilityThe Materials International Space Station Experiment Flight Facility is a hardware platform on the exterior of the ISS that provides exposure to the harsh space conditions for the accelerated testing of materials and technologies with important applications both in space and on Earth. This ISS National Lab commercial facility is owned and operated by Aegis Aerospace., an in-orbit platform from Alpha Space Test and Research Alliance deployed externally onboard the ISS.
The Purdue researchers will 3D print samples of stainless steel, nickel metal alloys, and metal oxides (ceramics) such as titania or zirconia to be launched to the ISS. Upon arrival, the samples will be mounted on the MISSE Flight Facility, where they will remain for six months. During this time, the samples will be exposed to the harsh conditions of space including high-energy radiation, debris impact, extreme heat and cold cycling, ultrahigh vacuum, and atomic oxygen.
Once the samples are returned to Earth, the research team will analyze the samples to determine whether the 3D printed metals and metal oxides are better suited to withstand high radiation levels and debris impact compared with conventionally formed metals and ceramics.
Unique Microstructure From 3D Printing
The Purdue research team found they were able to produce a unique microstructure within metals and ceramics when they 3D printed and heat-treated samples. Nearly all metals are made up of a patchwork of crystals, called grains, that form the microstructure and provide strength to the material but also create boundaries where fractures can occur. These grains can be seen in the large blotches of different shades of grey in galvanized steel fence posts or guard rails.
The microstructure of the 3D printed metals produced by Purdue is composed of nano-sized grains too small to see even with an optical microscope. Nanostructured grains with controlled defects have been shown to provide increased strength and hardness. Radiation significantly reduces the usable life of most materials—polymers break down and metals become brittle. However, nanostructured grains can mitigate many of the effects of radiation damage by controlling where radiation damage occurs. The boundaries between grains act as a sink for radiation damage and limit the damage to the overall strength of the metal. Thus, there is potential for these nanostructured metals to have prolonged life in high-radiation environments where other metals would become brittle and fail.
In their ISS National Lab investigation, the Purdue research team will examine whether nanostructured grains make their 3D printed metals more resilient against high levels of radiation. The team will also explore whether their nanostructured metal oxides (ceramics) can withstand high-velocity impact from debris in low Earth orbit(Abbreviation: LEO) The orbit around the Earth that extends up to an altitude of 2,000 km (1,200 miles) from Earth’s surface. The International Space Station’s orbit is in LEO, at an altitude of approximately 250 miles..
From Nuclear Reactors to Deep Space Exploration
If the 3D printed metals are found to be radiation-resistant, the Purdue research team seeks to apply the metals to two very different applications: 1) deep-space satellites and spacecraft and 2) nuclear reactors on Earth. While the types of radiation vary significantly, both applications are subject to very high radiation levels.
For nuclear reactors, radiation-tolerant metals could enable next-generation reactors that are safer and more efficient. The metals could also be applied to existing reactor technologies to prolong the life of critical components and decrease costly and hazardous maintenance. For deep space exploration, the use of radiation-tolerant metals could prolong missions by extending the life of mission-critical components on satellites or spacecraft. Nanostructured ceramics could also provide protection against meteoroid impact. Furthermore, back on Earth, this same ceramic technology could translate to important defense applications.
“The Purdue research team is opening up new material solutions to some of the most extreme environments on Earth and in space,” said Dr. Ryan Reeves, program director of advanced materials at the Center for the Advancement of Science in Space, manager of the ISS National Lab. “The team is doing this by not only 3D printing metals on demand but also infusing them with enhanced mechanical properties such as radiation protection through nanostructured grains.”
Media Contact:
Patrick O’Neill
904-806-0035
PONeill@ISSNationalLab.org