New Study on the Space Durability of 3D-Printed Nanocomposites
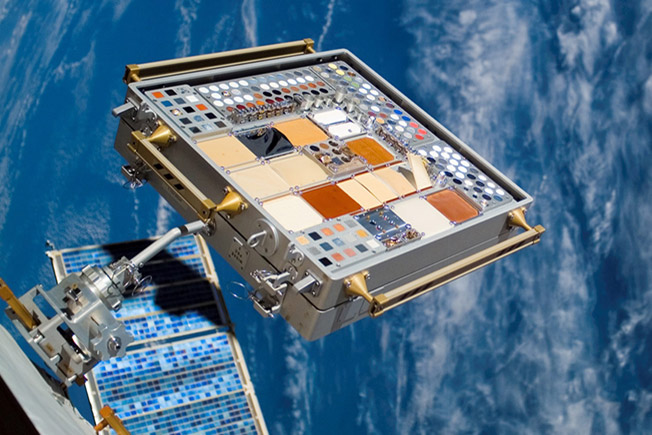
Media Credit: NASA
October 1, 2020
Thermoplastics such as Kapton or Teflon, which become soft when heated and harden when cooled, are used in aerospace applications such as wire insulation, thermal blankets, and metal surface coatings. However, these materials are known to degrade with prolonged exposure to the harsh conditions of space. A new study by the University of Illinois Urbana-Champaign (UIUC) will leverage the International Space Station (ISSInternational Space Station) to determine whether a new class of 3D-printed polydicyclopentadiene (pDCPD)-based thermosetting polymers, which irreversibly harden when heated, may provide a more durable option for space-based applications.
The UIUC team seeks to examine the durability of the pDCPD polymers, copolymers, and composites—produced by integrating new polymer formulations, 3D printing, and a rapid polymer curing technique—when exposed to the extreme conditions outside the ISS.
This investigation was awarded through an ISS U.S. National Laboratory solicitation for flight experiments that use the MISSE Flight FacilityThe Materials International Space Station Experiment Flight Facility is a hardware platform on the exterior of the ISS that provides exposure to the harsh space conditions for the accelerated testing of materials and technologies with important applications both in space and on Earth. This ISS National Lab commercial facility is owned and operated by Aegis Aerospace., an in-orbit platform from Alpha Space Test and Research Alliance deployed externally onboard the ISS.
Novel Materials for Space Applications
As a lightweight thermoset material, pDCPD is used in manufacturing applications such as heavy automobile body panels and aviation components. UIUC has been exploring composite fabrication technologies for pDCPD that may yield benefits in energy savings and rapid production for ground-based manufacturers and also enable new space-based applications for the polymers.
Frontal polymerization is a process in which the polymerization, a chemical reaction joining monomer molecules together to form polymers, propagates through the reaction medium in waves. This offers an energy-saving approach to polymer synthesis by taking advantage of a self‐propagating exothermic reaction to accomplish rapid curing of the material. By integrating frontal polymerization with 3D printing to produce pDCPD, UIUC hopes to provide a rapid, in-situ resource utilization manufacturing method that can be efficiently used in space or on Earth.
UIUC’s study on the ISS will provide quantitative data on material erosion that will help determine if this new class of pDCPD thermosetting polymers can better withstand the harsh space environment when compared with currently used thermoplastics. The cross-linked matrix structure of pDCPD gives the polymer high impact and corrosion resistance, and the pDCPD composites to be tested on the ISS will be prepared by including small amounts of silica nanoparticles in the material formulations to enhance erosion resistance.
Exposure to Actual LEO Conditions
By working with the ISS National Lab to bring their research to the ISS, the UIUC team is able to ensure that their pDCPD-based materials are tested in the actual low Earth orbit(Abbreviation: LEO) The orbit around the Earth that extends up to an altitude of 2,000 km (1,200 miles) from Earth’s surface. The International Space Station’s orbit is in LEO, at an altitude of approximately 250 miles. (LEO) environment. This is important for deriving accurate erosion yields and degradation rates for the polymers and composites. Ground-based simulation facilities are unable to accurately replicate the range of conditions that are most important for studying degradation mechanisms—including exposure to atomic oxygen, micrometeoroids, ultraviolet radiation, and extreme thermal cycling.
UIUC will synthesize the test materials in ground laboratories and then launch the materials to the ISS for LEO exposure on the MISSE Flight Facility for a minimum of six months, after which the materials will be returned to Earth for post-mission analysis. The study is jointly supported by an Air Force Office of Scientific Research (AFOSR) grant to UIUC and by the ISS National Lab.
“The innovative coupling of selective high-temperature synthesis with 3D printing by UIUC offers a pathway for utilization of space or Earth in-situ resources in the manufacture of new materials,” said Dr. Etop Esen, commercial innovation manager at the Center for the Advancement of Science in Space (CASIS(Abbreviation: CASIS™) The nonprofit organization that manages the ISS National Lab, which receives at least 50 percent of the U.S. research allocation on the International Space Station to facilitate research that benefits humanity (NASA manages the other 50% and focuses on research for space exploration purposes).), manager of the ISS National Lab. “This project will determine if the pDCPD polymers produced by this method are more durable than conventionally manufactured polymers, such as Kapton or Teflon, currently used in harsh aerospace applications.”
Media Contact:
Patrick O’Neill
904-806-0035
PONeill@ISSNationalLab.org